Die Casting Fundamentals Explaineds
Wiki Article
Top Guidelines Of Manufacturing Industries
Table of ContentsThe Facts About Lean Production UncoveredMfg Can Be Fun For EveryoneSome Ideas on Mfg You Need To KnowGetting The Lean Production To WorkThe Definitive Guide for OemSome Known Details About Additive Manufacturing
The message on this page is a sample from our full White Paper 'Shot Moulding for Customers' - * Sample message * - for full guide click the download button above! Intro This overview is intended for individuals who are aiming to resource plastic mouldings. It offers a much required understanding right into all that is included with producing plastic parts, from the mould tool needed to the moulding process itself.If you want to explore even more, the guide covers types of mould tools, in addition to special completing procedures such as colours & plating. Words that are highlighted can be discovered in the glossary in the appendix ... Component I: Moulding: The Essentials The Benefits of Shot Moulding Plastic shot moulding is a really accurate procedure that offers a number of benefits over other plastic handling methods.
Accuracy is ideal for extremely detailed components. You can hold this moulding in the palm of your hand and it has bosses, ribs, metal inserts, side cores and openings, made with a moving closed off attribute in the mould device.
The Ultimate Guide To Mfg

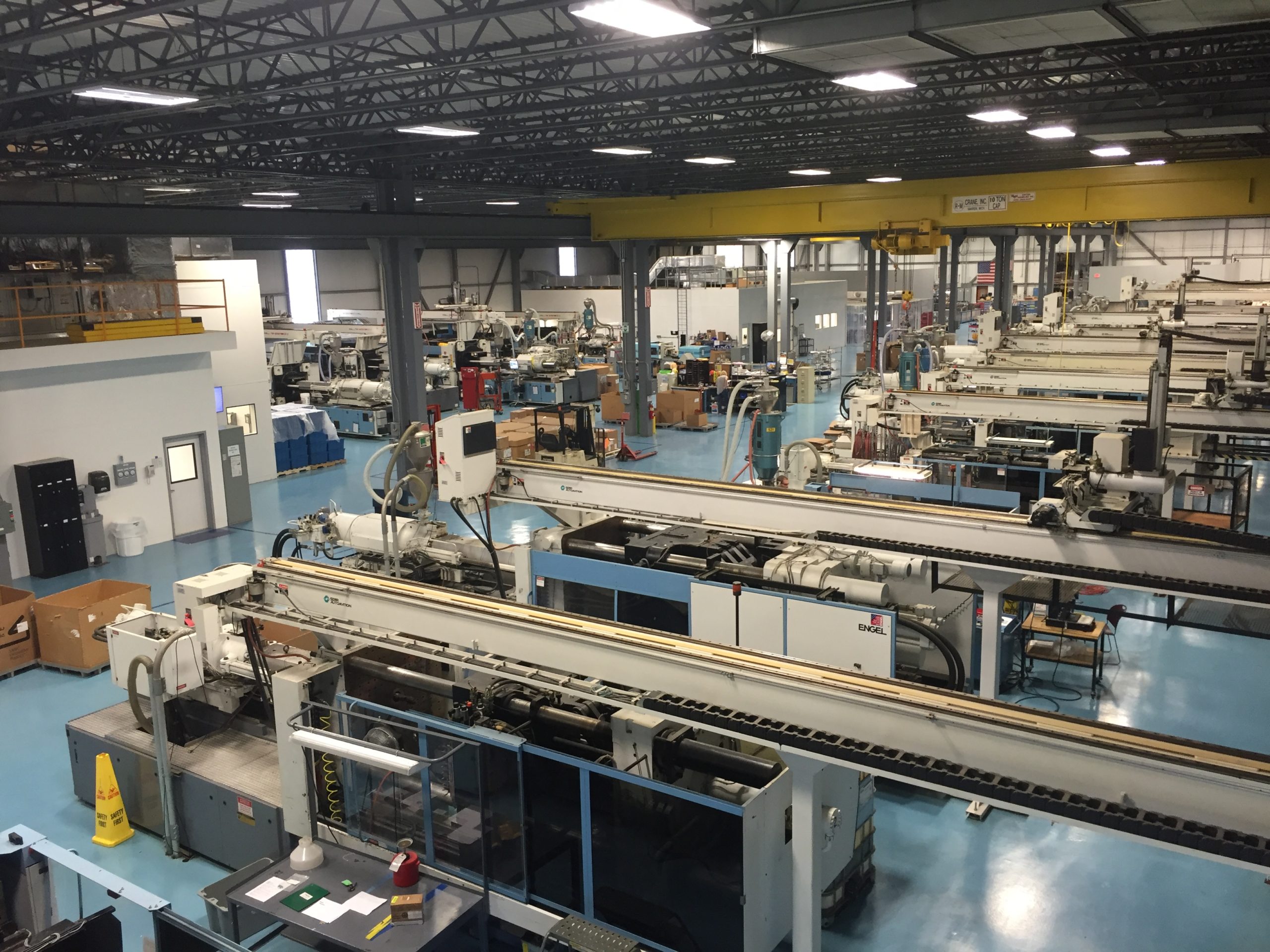
from material feed & melting; material injection; cooling time and ejection to the re-closing of the mould tool ready for prepared next cycle. Draft angles - The walls of a moulded part should be slightly tapered in the instructions in which the component is expelled from the mould tool, to enable the component to be expelled easily.
Ejector stroke - The pushing out of ejector pins to eject the moulded part from the mould tool. Ejector stroke speed, length and also timing requires to be thoroughly controlled to avoid damages to the ejectors and also mould tool, however at the very same time make the moulding cycle as brief as feasible.

A Biased View of Lean Production
Ribs - When a plastic component has slim walls, ribs are contributed to the layout to make the slim wall surfaces stronger Side cores - Side activity which creates a function on a moulded part, at an opposing angle to the regular opening instructions of the mould device. additive manufacturing. The side core needs to be able to withdraw as the plastic part can not be expelled or else.
Walls - The sides of a moulded part The text on this web page is an example from our complete White Paper 'Shot Moulding for Purchasers'.
Shot moulding is commonly used for making a variety of components, from the smallest parts to entire body panels of autos. Advancements in 3D printing innovation, utilizing photopolymers that do not thaw throughout the injection moulding of some lower-temperature thermoplastics, can be made use of for some straightforward injection moulds. Injection moulding utilizes a special-purpose machine that has three parts: the injection unit, the mould and the clamp.
The smart Trick of Additive Manufacturing That Nobody is Talking About
Process qualities [modify] Injection moulding uses a ram or screw-type plunger to require liquified plastic or rubber material right into a mould tooth cavity; this solidifies right into a form that has actually complied with the contour of the mould. It is most frequently made use of to refine both thermoplastic as well as thermosetting polymers, with the volume used of site web the former view it now being considerably higher.: 13 Thermoplastics are prevalent because of attributes that make them highly appropriate for shot moulding, such as convenience of recycling, convenience for a wide range of applications,: 89 as well as capacity to soften and move on heating.In several tooth cavity moulds, each tooth cavity can be the same and create the very same parts or can be one-of-a-kind and form multiple various geometries during a solitary cycle.
The screw provides the raw material forward, mixes as well as homogenises the thermal and also thick circulations of the polymer, and lowers the called for home heating time by mechanically shearing the product and adding a substantial amount of frictional heating to the polymer. The product feeds ahead via a check valve and collects at the front of the screw into a quantity known as a shot. When enough product has gathered, the product is required at high stress and velocity into the component forming tooth cavity. The exact amount of contraction is a function of the material being used, as well as can be fairly predictable. To stop spikes in pressure, the procedure usually uses a transfer setting representing a 9598% full dental caries where the screw changes from a consistent velocity to a constant pressure control.
How Lean Manufacturing can Save You Time, Stress, and Money.
When the screw reaches the transfer setting the packing stress is used, which finishes mould filling as well as makes up for thermal contraction, which is fairly high for thermoplastics about several other products. The packing stress is used until the entrance (tooth cavity entrance) strengthens. Because of its small dimension, eviction is usually the initial area to solidify via its entire thickness.: 16 Once the gateway strengthens, say goodbye to product view it can enter the tooth cavity; appropriately, the screw reciprocates and also acquires material for the next cycle while the material within the mould cools so that it can be expelled and also be dimensionally steady.Report this wiki page